Purpose
The intended purpose of this article and alert is to warn people about the dangers of loading and unloading elevating work platforms, or EWPs, into and off tilt tray trucks.
Background
An EWP slipped and fell down the tray of a tilt tray truck, causing an incident in Queensland in 2009. The operator was in the basket and used the EWP to load and place the tilted tray into the vehicle for transportation.
The truck tray intended for the EWP’s transport was too short to allow it to be placed in the proper transport (stowed) position without the basket overhanging the tray. As expected, the EWP with the basket was dangling and overhanging over the tray. To prevent overhanging, the basket was rotated beneath the boom (‘crowded’ position).
The braked wheels closer to the basket lifted off the tray when the basket was put in the crowded position and positioned onto the tilted tray. Brakes were not fitted on the remaining wheels in contact with the tray.
The winch cable was not linked to the EWP, allowing it to slide and roll down the tray’s slope. The basket of the EWP hit the ground as a result of this movement. The operator was crushed between the handrail of the basket and the ground, causing severe injuries.
Actions Required To Minimize The Risk Of Injury
Working with EWPs can pose a severe threat to one’s health and safety. You must remove these dangers and risks or minimize them to the greatest extent possible.
The following must be ensured and guaranteed for the safe loading of EWPs:
- The EWP should be loaded and unloaded as per the EWP manufacturer’s instructions.
- Unless the manufacturer’s directions and specifications allow it to be driven, always winch the unmanned EWP on and off the tilt tray.
- Use the winch if the tray’s slope is too steep or if the tray surface or EWP tires are slick and slippery.
- The truck must stay on flat or firm terrain and ground with no side slopes. Loading in a side slope during slick circumstances may potentially lead to the winch being unable to keep the EWP from slipping off the tray.
- The truck is appropriate and suitable for transporting the EWP in the travel (stowed) position set by the ETW Manufacturer. In the travel (stowed) position, the trailer or tray should be long enough for the boom and basket. The EWP’s mass must be within the winch’s, truck’s, and trailer’s capability.
- Operators of EWPs should be trained and given operating instructions before they handle and use them. Training is incredibly crucial and necessary to load and unload EWPs onto and off tilt trays.
- The EWP is transported following the regulations and requirements of the Department of Transportation and Main Roads.
Additionally, it would be best if you also considered the following factors:
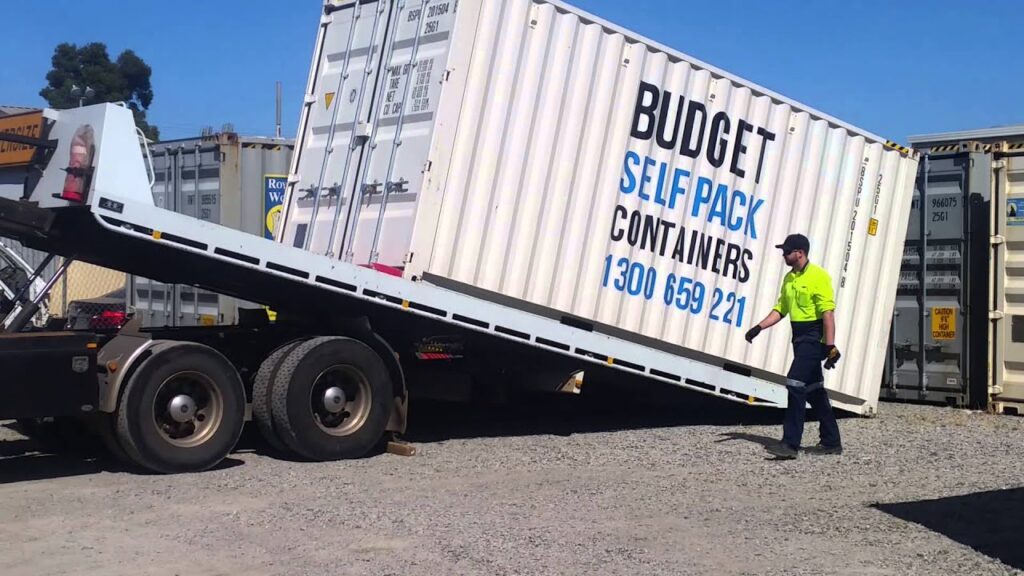
- Rather than using a tilt tray truck, transport EWPs using a drop deck trailer (low loader).
- Another individual should use the winch while the EWP is driven up or down the slope of the tray.
- If the manufacturer recommends placing the basket on the tray, level the tilt tray before placing the basket on the tray.
- When placing the basket on the tray, use the ground controls.
- Ensure that proper protective gear and equipment are always available for all workers and personnel.
Routine Maintenance
A qualified and competent tilt tray company in Bunbury should inspect the essential components at least once a year or as specified by the manufacturer. A preventative inspection, testing, and maintenance program will aid in the safe operation of the EWPs.
Ensuring that workers have access to the knowledge, training, guidance, and supervision is also needed to carry out their works and jobs safely. It includes but is not limited to or restrained to the inspection and examination of the winch, tie-down points, chains, winch cable, and EWP brakes.
Aside from that, inspect for improper adjustments, inefficient brakes, correct loading capacity, uncontrolled motion, loose connections, broken wire ropes, and damage to steps or ladders. Be on alert for any flaw or irregularity.
Inspections are done on an ‘hours of use’ basis to avoid any accidents. A record of the activities above should be kept to provide and give a history of the plant. Ensure that all concerns and repairs are reported before use.
Any equipment that is not working correctly during inspection or has sustained damage to its critical components should not be used until repaired by a qualified mechanic.
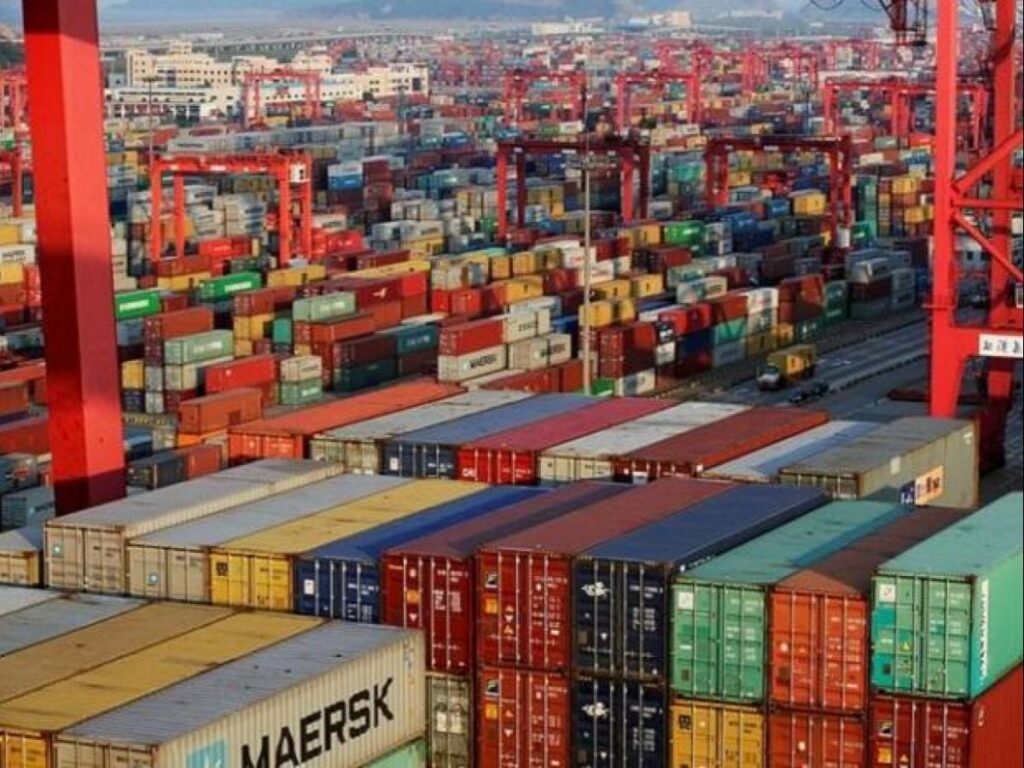
Legislative Requirements
All individuals operating a business, like Reef Group Bunbury, whether as an employer, self-employed person, supplier, manufacturer, designer, installer, or owners of plant and personnel, are subject to the Work Health and Safety Act 2011. The law protects all workers by setting up requirements and standards aimed at building safe and healthy workplaces. It assists businesses in making sure that safety issues are resolved and dealt with fairly.
The law subjects the responsibilities and duties of safety to business owners, managers, supervisors, and workers at the workplace. Its primary purpose is to manage the risks and hazards in a work environment and provide an equivalent and higher health and safety standard.
The purpose of the information in this alert is to assist individuals in fulfilling their responsibilities related to managing risks associated with loading and unloading EWPs for transportation reasons and purposes.